Когда говорят о радиографическом контроле, чаще всего имеют в виду метод проверки качества изделий, не разрушая их. Он нужен, чтобы заглянуть внутрь материалов и понять, всё ли с ними в порядке. В промышленности это особенно важно, ведь дефект, незамеченный вовремя, может привести к серьёзным последствиям. Сварные соединения, отливки, трубопроводы — всё это проверяется радиографией. Используется такой метод на заводах, стройплощадках, в энергетике, судостроении и даже в авиации. Радиографический контроль работает по принципу, похожему на то, как делают рентгеновские снимки человеку в больнице. Только здесь речь не о костях, а о металле, пластике, керамике и других материалах. И если на снимке врач ищет перелом, то специалист по неразрушающему контролю — поры, трещины, шлаковые включения и прочие дефекты, способные повлиять на надёжность конструкции. Часто его заказывают для проверки сварки — это, пожалуй, самая типичная задача. Те, кто хотя бы раз пытался заказать радиографический контроль, знают, что это требует особого подхода: нужно соблюдать правила безопасности, подобрать нужное оборудование, правильно интерпретировать результаты. Это не просто «сделать снимок», это целый технологический процесс.
Суть метода в том, что через объект пропускается излучение, чаще всего рентгеновское или гамма. Излучение проходит через материал, а затем попадает на чувствительный экран, пленку или датчик. На своём пути лучи теряют энергию, и насколько сильно они ослабнут — зависит от плотности и толщины материала, через который они проходят. Если внутри объекта всё однородно, то изображение получится равномерным. А вот если в металле есть, например, пустоты, то они пропустят больше излучения. Это проявляется как более тёмные участки на снимке. Благодаря этому специалист может понять, где есть дефекты и насколько они серьёзные. Рентгеновское и гамма-излучение — вещи опасные, поэтому работу проводят с соблюдением норм радиационной безопасности. Гамма-источники, кстати, удобны тем, что не требуют питания от электросети и могут использоваться в полевых условиях. Но у них есть срок службы, связанный с распадом радиоактивных изотопов. Изображение может фиксироваться как на классическую пленку, так и в цифровом формате. Цифровая радиография даёт возможность быстрее получать результат, хранить его в архиве и обрабатывать с помощью программ. Это особенно ценно на крупных производствах, где важно оперативно выявлять и устранять дефекты.
Оборудование и материалы
Оборудование для радиографического контроля можно условно разделить на три части: источники излучения, приёмники (детекторы) и вспомогательные средства. Источники бывают рентгеновскими и гамма. Рентгеновские аппараты подключаются к электросети, у них регулируются напряжение и ток, что позволяет подстраиваться под толщину объекта. Такие аппараты бывают переносными, настольными или стационарными — всё зависит от задач.
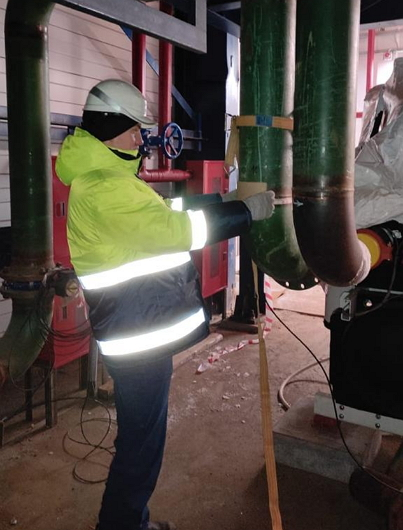
Гамма-источники основаны на использовании радиоактивных веществ, таких как иридий-192 или кобальт-60. Эти материалы излучают сами по себе, и не требуют электричества. Это удобно, если нужно провести контроль в условиях, где подключение техники проблематично. Но с ними строго регулируется хранение, транспортировка и утилизация. Контейнеры для перевозки таких источников делаются из свинца или других тяжёлых материалов, чтобы не допускать утечки излучения. Приём информации осуществляется с помощью рентгеновской плёнки или цифровых детекторов. Плёнка — классический и всё ещё широко применяемый способ. Она бывает разной чувствительности и толщины, требует проявки, фиксации и сушки. Весь процесс похож на фотолабораторию.
Цифровые технологии включают в себя устройства типа CR (Computed Radiography) и DR (Digital Radiography). В первом случае используется фотопластина, которая сканируется для получения изображения, во втором — изображение сразу попадает на экран. Цифра даёт возможность моментально просмотреть снимок, увеличить интересующие участки, провести анализ, сохранить в базе данных. Но и стоит всё это дороже. Вспомогательное оборудование тоже важно: защитные ширмы, экраны, штативы, держатели для источников, кабели, свинцовые буквы для маркировки снимков, дозиметры для измерения уровня радиации. Обязательно используются индивидуальные средства защиты: свинцовые фартуки, перчатки, очки, а иногда и специальные кабины или укрытия. Безопасность — ключевой элемент в этой работе. Используемые материалы могут включать калибровочные образцы, которые нужны, чтобы проверить качество и чувствительность снимка. Это металлические пластины с имитацией дефектов. Они помогают понять, насколько хорошо оборудование настроено и можно ли доверять полученному изображению.
Методика проведения контроля
Чтобы получить снимок, на котором действительно будет видно то, что нужно, недостаточно просто включить аппарат и навести его на деталь. Всё начинается с подготовки. Объект должен быть очищен от грязи, ржавчины, шлака и краски в зоне контроля — то есть там, где будет проходить излучение. Если поверхность загрязнена, изображение получится размытым, а некоторые дефекты могут вообще не проявиться. Важно ещё правильно зафиксировать изделие — чтобы оно не двигалось во время экспозиции, особенно если используется длинная выдержка.
Подбираются параметры съёмки в зависимости от материала, его толщины, конструкции изделия и предполагаемых дефектов. Специалист определяет, какое напряжение подать на рентгеновскую трубку или какой гамма-источник использовать. Также учитывается чувствительность плёнки, время экспозиции, расстояние между объектами. При неправильном выборе параметров можно либо не заметить дефект, либо «пережечь» снимок — он будет слишком тёмным и бессмысленным. Всё это требует опыта и знания стандартов.
Расположение элементов системы играет ключевую роль. Обычно выстраивается прямая линия: источник излучения — объект — детектор. Но в некоторых случаях используется косое или даже двойное просвечивание. Расстояние между ними подбирается так, чтобы лучи максимально эффективно проходили через интересующий участок. Иногда приходится изощряться, особенно если объект громоздкий, сложной формы или стоит в неудобном месте. Детектор (например, плёнка) должен быть расположен ровно, без изгибов, потому что даже небольшое отклонение может привести к искажению размеров дефектов. После съёмки материал (если это плёнка) проявляют, фиксируют и сушат. Процесс строго регламентирован: температура растворов, время экспозиции и даже качество воды имеют значение. Плохо проявленная плёнка — это испорченный результат, который придётся переделывать. Цифровые методы упрощают этот этап, потому что изображение появляется на экране почти мгновенно. Однако анализировать его вручную всё равно нужно — автоматика не заменит человеческий глаз. Интерпретация — сложный этап. Специалист смотрит на снимок, сопоставляет затемнённые участки с чертежом объекта и решает: есть ли там дефект и насколько он критичен. Он должен уметь отличить артефакт проявки от реальной трещины, а тень от болта — от полости в сварном шве. Требуется не только зрительная внимательность, но и знание норм. Часто приходится использовать увеличительное стекло, линейку или даже специализированное программное обеспечение, если снимок цифровой.
Типы выявляемых дефектов
Радиографический контроль позволяет выявить множество дефектов, которые скрыты внутри материала. Один из самых серьёзных — это трещины. Они бывают продольными, поперечными, сквозными и поверхностными. В радиографии трещина выглядит как тонкая, тёмная линия. Она может быть едва заметна, особенно если идёт под углом к плоскости съёмки. Опытный специалист сразу различит, настоящая это трещина или просто царапина на поверхности плёнки.
Поры — ещё один частый дефект, особенно в сварных соединениях. Это маленькие пузырьки газа, застрявшие в металле во время сварки. На снимке они выглядят как круглые или овальные тёмные пятна. Если пор много, они могут сливаться, образуя скопления. В зависимости от расположения и размера, они могут считаться либо допустимыми, либо опасными. Непровары — это участки, где металл не проварился до конца. Это очень критичный дефект, потому что он снижает прочность соединения. Обычно они проявляются как узкие тени вдоль шва, порой их трудно заметить. Часто их путают с линиями от отблесков на плёнке, и тут важен опыт оценщика. Включения — это чужеродные материалы, попавшие в металл. Шлак, окалина, песок, иногда даже кусочки электрода. Они имеют другую плотность, чем основной материал, и потому видны на снимке. По форме и оттенку можно примерно понять, что это за включение. Иногда специалисты составляют целые библиотеки снимков с типичными дефектами — чтобы новички могли учиться распознавать их. Например, характерный снимок с пористостью в виде цепочки пузырей в алюминиевом шве, или тёмная полоска вдоль корня шва — это непровар. Такие образы помогают быстро ориентироваться в реальной практике.
Критерии оценки зависят от стандартов: ГОСТ, ISO, ASME — у каждого свои требования. Одни дефекты считаются допустимыми при определённой длине и расстоянии между ними, другие недопустимы вообще. Например, трещины — это всегда брак, независимо от их длины. Поры могут быть допустимы, если их диаметр меньше определённого значения и если они не сливаются в группы. Классификация проводится по градациям качества: уровень А, В, С и т.д., где «А» — наивысший. Кстати, некоторые заказчики требуют особо жёстких условий, даже выше норм — особенно если изделие пойдёт в авиацию или атомную энергетику. Ошибки в оценке могут стоить дорого: недооценённый дефект — это риск аварии, а переоценённый — лишние расходы на переделку. Поэтому ответственность специалиста велика, и все его решения должны быть обоснованы и зафиксированы в отчёте.
Добавить комментарий
Для отправки комментария вам необходимо авторизоваться.